Implementation of an energy
management system at
Toshiba
How Toshiba reduced its energy consumption by 50% in 1 year
The Toshiba Dieppe site has made huge energy savings after
renewing its chillers and air compressors. And thanks to the MyDametis platform,
teams are more autonomous when it comes to energy management.
“We called on Dametis in 2020 to carry out a project whose aim was to reuse energy from our processes to heat buildings. In the first year, we reduced our gas consumption by 50%. The MyDametis tool gave all our staff easy access to their consumption data, which they could then analyze.”
Mohamed Mebtoul, Toner Department Manager
Toshiba, Dieppe
Watch the testimony of Mohamed Mebtoul, toner department manager at Toshiba’s French plant
RESULTS
Results in figures
-50%
in gas consumption in the services building in 2022, due to the recovery of waste heat from air compressors and chillers.
– 40 000€
of energy savings on the annual bill in 2022 thanks to early detection of deviations. The result: better control of total heat energy
– 15%
in total heat energy consumption thanks to better optimization of heating control (scheduling, etc.) via MyDametis software and its energy management system.
641 MWh
saved over 2022
146 T eqCO2
saved over 2022
CONTEXT
Toshiba Dieppe, leader in
toner ink production
A giant in the manufacture of electronic and IT equipment, Toshiba also offers solutions in data storage, energy and infrastructure.
Toshiba Dieppe is one of the Japanese group’s two largest toner ink production sites worldwide. The site opened in 1986, and started out assembling photocopiers. In 1993, he began producing toner ink: spraying, plastic injection, bottling and cartridge assembly.
Toshiba Dieppe in figures
230
employees on site
30M€
in sales
ISO-certified
ISO 9001, ISO 14001 et ISO 45001
Certified
“Industry of the Future Showcase”
1986
Based in Dieppe for over 35 years
The site comprises 3 buildings
Toner building
Toner manufacturing building. Includes 2 chillers for machine cooling and 7 air compressors.
Building dedicated to finished product logistics.
CHALLENGES
Overheated chillers and
worn air compressors
Overheating Chiller Units
The Toner building is dedicated to the manufacturing of toner cartridges. During the process, the machines generate a lot of heat. To prevent any risk of overheating, two chiller units condition the air and maintain the production circuit at the right temperature.
However, a problem arose: the chiller units started showing signs of fatigue, especially during heatwaves. This issue is critical for the Toshiba Dieppe site as the cold production must never be interrupted.
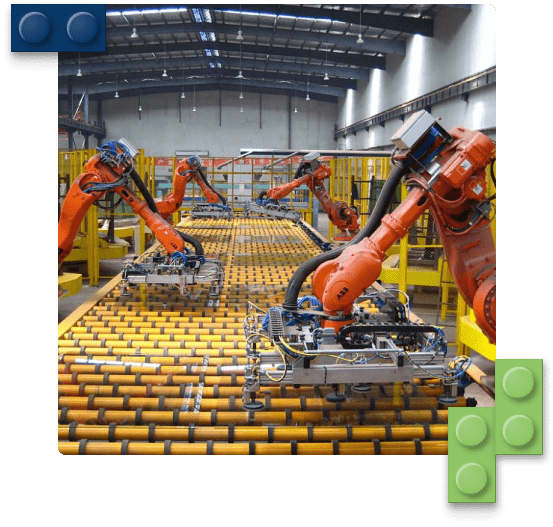
Installation of new
chillers
The priority was to replace the two chillers at the end of their cycle. Dametis installed two new ones to ensure and sustain cold production.
Chillers condition the air temperature by removing heat from the cooling area. Dametis recovers this heat to convert it into energy.
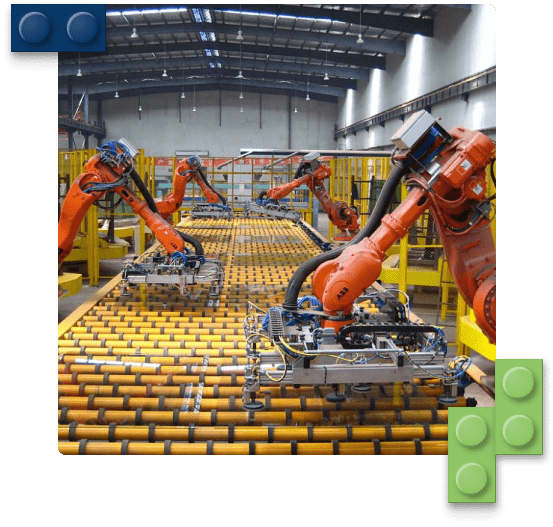

Worn-out and energy-consuming air compressors
At the same time, air compressors also began to underperform. As a result, their energy consumption was increasingly weighing on the energy bill.
Toshiba Dieppe needed to improve energy performance by renewing its air compressors in addition to its chillers.

Installation of new
compressors
Dametis has installed two new air compressors in the Toner building.
In order to optimize energy usage, Dametis has installed a heat exchanger that recovers the waste heat produced by the air compressors and chillers. This heat is then used as an energy source to heat the Services building dedicated to photocopier assembly.
Inadequate tools for energy management
As part of the signing of an Energy Performance Contract (EPC), Toshiba Dieppe had to achieve specific energy efficiency targets.
To monitor the site's energy consumption, the teams were using inadequate and impractical tools and modules. As a result, collecting, analyzing, and correlating each data point was time-consuming, tedious, and repetitive.

Energy Management
Faster and Easier
Dametis proposed to Toshiba to use its collaborative platform MyDametis. Thanks to this tool, teams can visualize real-time data related to compressed air consumption, chilled water, heating energy, and electricity consumption throughout the factory.
Centralized data, automated readings, comprehensive performance reports, intuitive interface: MyDametis simplifies teams' daily tasks, saves them valuable time, and makes them more independent in energy management.
Moreover, an alarm module triggers an alert as soon as a deviation is detected on the site. The tool notably identified an abnormal consumption level on a machine, which was then replaced.

RESULTS
The results of the implementation of an energy management
-50%
system for gas consumption in the services building in 2022 are due to the recovery of waste heat from air compressors and chillers.
– 40 000€
of energy savings on the annual bill in 2022 thanks to early detection of deviations. The result: better control of total heat energy
– 15%
consumption thanks to optimized heating control (timetabling, etc.) via MyDametis software.
641 MWh
saved over 2022
146 T eqCO2
saved over 2022
And your environmental transition,
shall we begin?
Dametis supports manufacturers like you in their transition
by controlling their consumption of energy, water and materials.
Book a call with an industry expert to discuss the challenges of
your industrial sites.

Raphaël Barbier
Case studies
See also
Agromousquetaires
View case study >
Alban Muller
View case study >
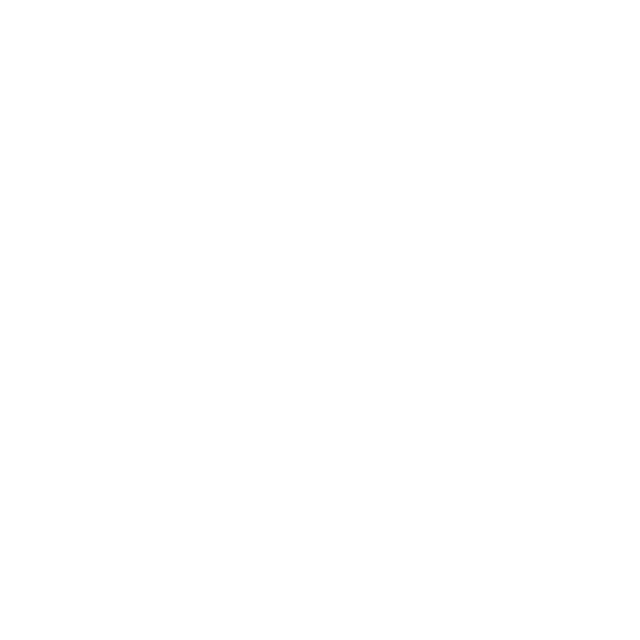
Coffee break
With a cloud of cream, milk, or simply black,
Enjoy our newsletter with your coffee, and learn how to accelerate your environmental transition!
Read more