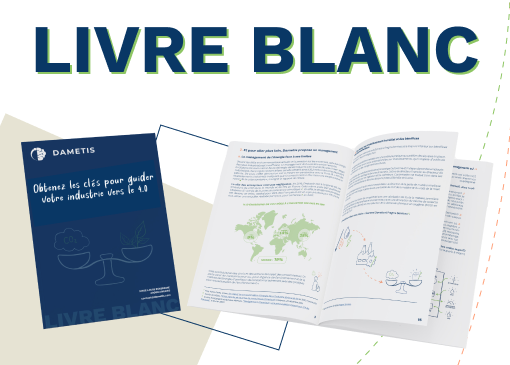
White Paper 1: Get the Keys to Guide Your Industry to 4.0
Decarbonizing the manufacturing industry is now a major challenge for economic, geopolitical, and environmental reasons. Energy Renovation and Renewable Energies: What actions should be implemented to achieve this? Energy Renovation and Renewable Energies: What actions should be implemented to achieve this?
To help you in this transition, we have written the Dametis White Paper in three chapters, so you can get the keys to guide your industry to 4.0!
This White Paper was made possible by Dametis experts:
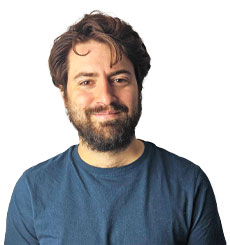
Julian Aristizabal
Co-founder, CEO
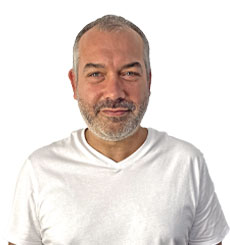
Jérémy Barrais
Product Manager
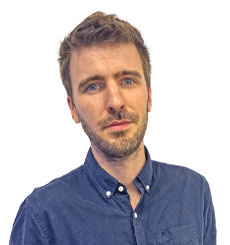
Nicolas Duran
Co-founder, CTO
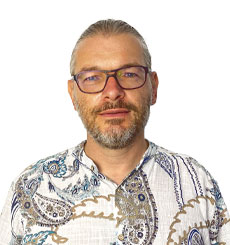
Sébastien Papouin
Technical Director
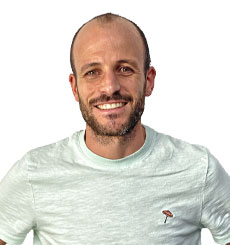
Cyril Quemeneur
Energy Engineer
Summary
> Chapter 1 – Data and Human Expertise at the Heart of Your Decarbonization Strategy
I. Environmental Memory and Intelligence (vs. Energy Memory and Intelligence)
II. Environmental Expertise in Software (vs. Expert Minds…)
III. 4.0 Data Artisans for Environmental Data (vs. Energy Data)
> Chapter 2 – A Collaborative Environmental Optimization Platform: A Must-Have for Your Transition
I. Maintaining Long-Term Performance
II. A Global Low or Zero Carbon Project
III. Impact on ESG Reporting (Environmental, Social, Governance Criteria)
> Chapter 3 – Managing Energy: Some Concrete Cases to Know Where to Start!
Chapter 1: Moving Towards Industry 4.0 – Data and Human Expertise at the Heart of Your Decarbonization Strategy
I. Environmental Memory and Intelligence
• An Already Outsourced ‘Energy Memory’
• The Limits of Excel Spreadsheets
Julian Aristizabal, CEO of Dametis: “Today, many industrial sites manage their energy with simple Excel spreadsheets. This involves the time-consuming and hazardous task of retrieving data – during plant tours5 , which in the absence of automated transmission can take 30 minutes or even an hour a day – and then integrating it, with a lot of copying and pasting, rewriting errors, stacking up versions created by different users… This method takes away precious time to reflect on these data (which are in any case incomplete and unreliable compared to those that would be returned by a good EMS).”
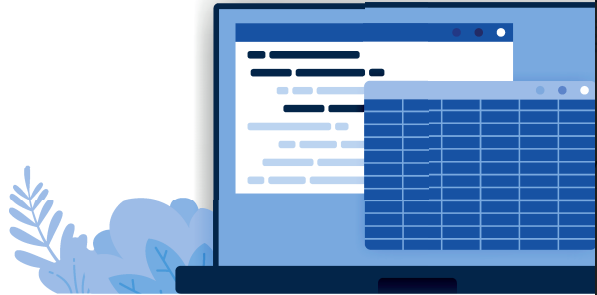
• Human and A.I. Together Facing the Ecological Challenge
Software to measure environmental performance is therefore (among other things) a new factory memory. When this software is sufficiently sophisticated, the data it contains is correct, well-organized and easy to access, contextualized and non-redundant. What’s special is that this memory can be mobilized simultaneously by two types of brain: human and algorithmic. While we should be concerned that, generally speaking, in our societies “the computer comes to represent an ideal in the light of which real thought perversely ends up appearing deficient” (Matthew B. Crawford)6, we must nevertheless recognize that the human mind cannot meet the challenge of industrial energy saving alone.
• Software Orchestras for ‘Environmental’ in the Factory of the Future
Software is already essential in today’s plants as they move towards the “minimum energy achievable” (MEA), and will become even more important as production sites become increasingly automated.
Programmable machine tools, welding and painting robots, remote-controlled forklifts, handling and assembly automatons have long been part of the factory and warehouse,” recalls Charles-Édouard Bouée in his book Confucius et les automates (ed. Grasset, 2014)7
.
But the new generation of this equipment will be nothing like the previous ones, because they will acquire more and more intelligence and, thanks to the Internet, they will be able to connect and communicate with each other.”
In Industry 4.0, environmental performance software will be the conductor of the ecological stakes in this “new cyber-physical reality”.
• Human Remains Essential
Julian Aristizabal, CEO de Dametis :
“The software is based on man-machine collaboration. Because in a factory, we always end up having to deal with exceptional situations, which again require human intervention. Software doesn’t create expertise; it works on the basis of human expertise written in algorithmic form. There are also things it can’t do, like (re)calibrating sensors8 – which inevitably drift over time, in other words, the zero shifts and the data returned is false.”
II. Environmental Expertise in Software
• ‘Expert Systems’ in the Service of Industrialists
• Challenging Factories Against the World’s Best Performances
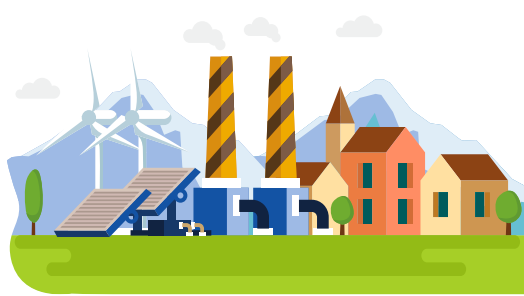
In addition, the expertise provided must be sufficiently rich to integrate the best environmental scores (energy among others) at world level, updated across all industries.
The EMS software can thus challenge utilities and processes by comparing them with the best performances worldwide. Of course, there’s no such thing as a pre-packaged repository that you can simply “pour” into the software… These data must be derived from the accumulated field experience (plant visits and audits, implementation and monitoring of measurement plans, etc.) of the company supplying the software, supplemented by specialized documentary research.
• Users of an EMS Can Enhance Their Energy Skills
III. 4.0 Data Artisans for Environmental Data
• Reflecting the life of the factory and eliminating “technical debts”
“I have visited factories where the software data was so disconnected from reality that the tool became unusable,” says Julian Aristizabal, CEO of Dametis. These technical debts concern, to varying degrees, 90% of the software I encounter.
What some software designers forget is that industrialists spend their time seeking solutions to concrete problems, and therefore modifying their installations. A software must reflect reality and take into account even the smallest changes that, over time, shape the factory.
• Examples of daily changes to consider
Would you like to obtain and read the rest of the White Paper to get all the keys to guide you towards Industry 4.0?
Fill out the form below ↓
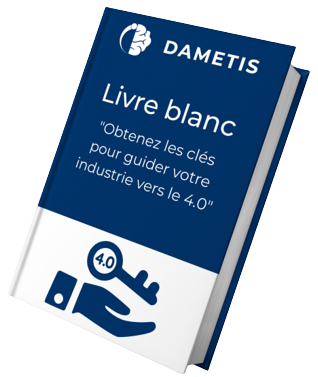