Your environmental
performance
brick by brick.
THE complete solution for optimizing the environmental performance of your plants to control costs, consume fewer resources, and reduce your carbon footprint.
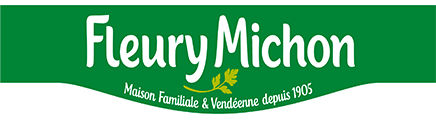
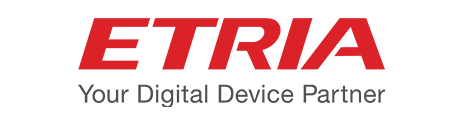
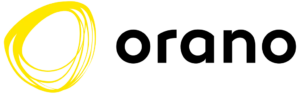
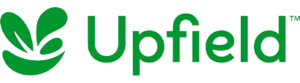
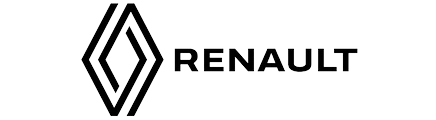
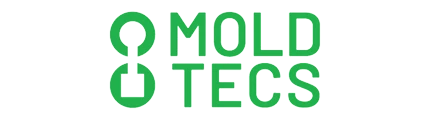
102 industrial groups already trust us
Consumer Goods
34%
Agribusiness
Cosmetics
intended for the production of domestic hot water
Control your bill
Optimize your resources
Anticipate and avoid the extra costs associated with malfunctions
Gain visibility to define a resilient strategy in the face of energy and water hazards
Build a multisite strategy
Help build a livable world
OPT FOR THE DIFFERENCE
Why entrust your challenges to Dametis?
International
we’re with you every step of the way, wherever you are.
The Dametis offer is 360. The ultimate solution that combines business expertise and software power.

MyDametis
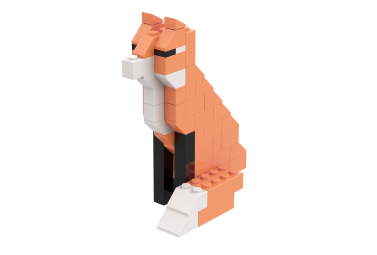
MyExpertise
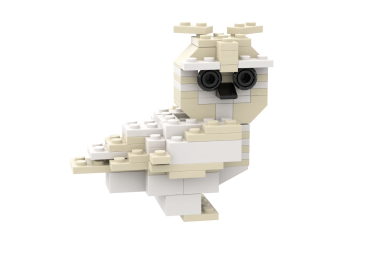
MyStrategy
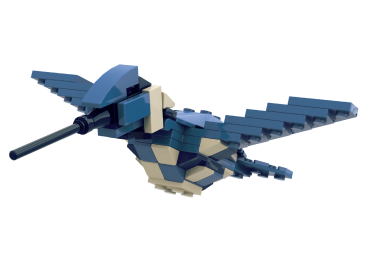
MyProject
Our labels and certifications for successful decarbonization
Dametis is mentioned in 5 Gartner reports, the leading consulting firm for actionable strategy and research, between 2022 and 2023.
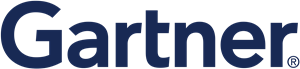
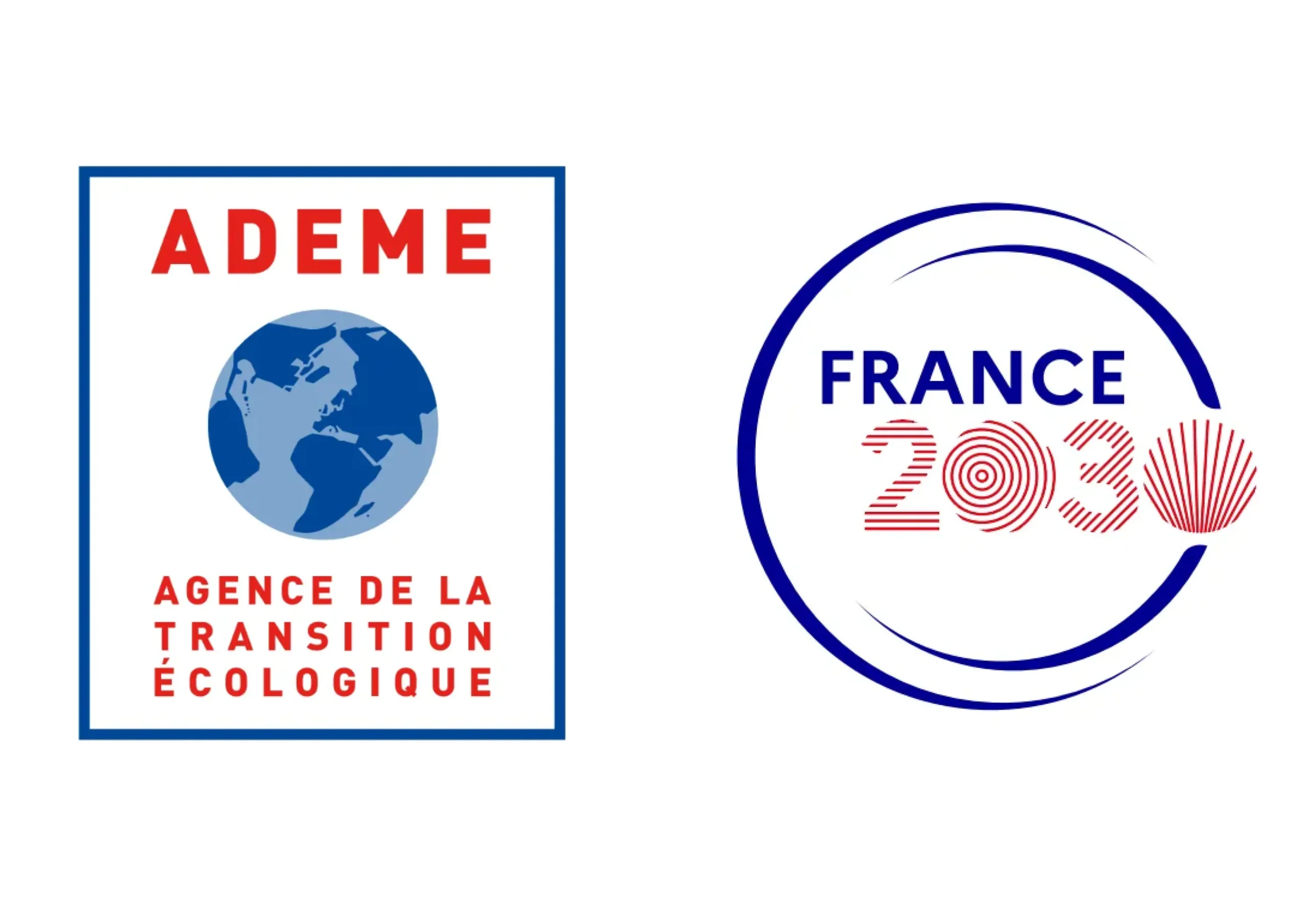
Dametis Winner of IBaC SME
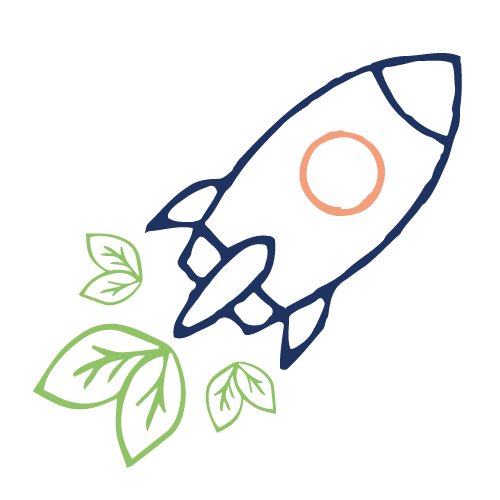
As part of the France 2030 program, Dametis is recognized by ADEME and ATEE for its commitment to the decarbonization of industry. This support will enable us to drive innovation in assisting industrial companies with their energy and environmental transition.
It all starts with our Lego theory
To make your factory as efficient as possible, we use the Lego theory.
The idea is simple: imagine your factory as an assembly of Lego blocks, each corresponding to a utility or process. Two similar blocks are comparable from one factory to another.
Thanks to this methodology, we can model each block and assign it an energy and environmental efficiency score according to our set standards.
Based on a map of your plant and your requirements, we define its ideal virtual version, block by block. This way, we know exactly which blocks to optimize to achieve excellent performance levels.
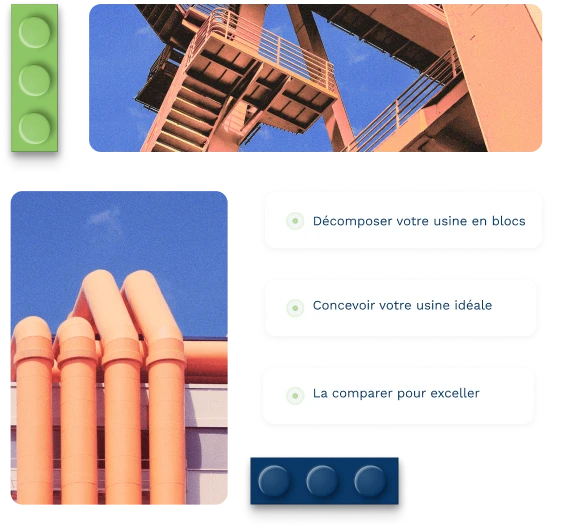
Become a player in the environmental transition
Why choose MyDametis?
Improving your industry’s environmental performance is becoming a real challenge in an ever-changing economic context.
MyDametis, c’est la seule plateforme pensée à 100% par des experts de la performance environnementale.
More than 40 companies are already using MyDametis on a daily basis to reduce their bills and greenhouse gas emissions.
Request a demo!
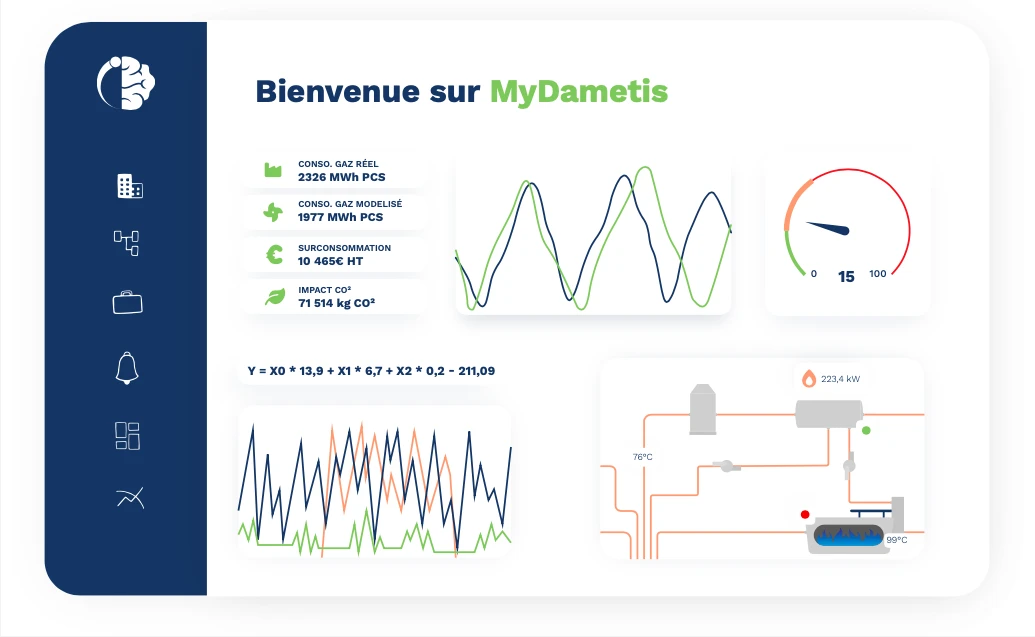
TESTIMONIAL
What they think of Dametis
Blog
Our latest articles
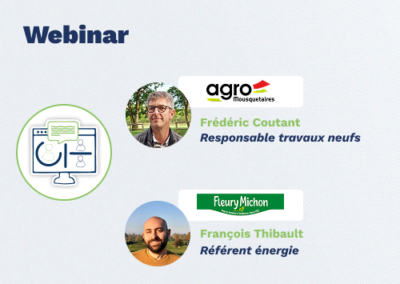
Webinar #5: How Etria optimizes its energy usage, reduces costs, and calculates the carbon footprint of its finished products
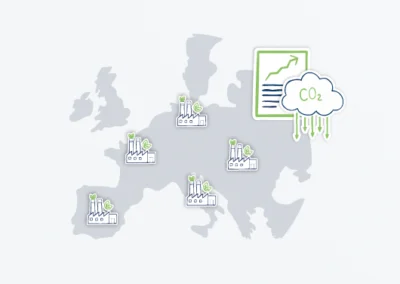
Clean Industrial Deal : l’Europe dévoile son business plan pour concilier décarbonation et compétitivité
Coffee break
With a splash of cream, milk or simply black, Enjoy our newsletter with your coffee to find out how you can accelerate your environmental transition!