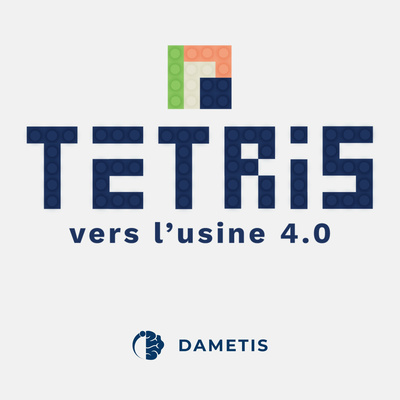
Episode 02 – Inventory: Simplified audit
Welcome to TETRIS, the way to Factory 4.0!
In this first season, you’ll discover our 5-step roadmap for improving your plant’s environmental performance.
Here are the 5 steps:
Step 1 – Taking stock to prepare the ground.
Step 2 – Detailed analysis, where we explore your plant in depth.
Step 3 – Adjustments to optimize your plant’s performance.
Step 4 – Guidelines and master plan, to define and structure your ideal factory.
Step 5 – Continuous improvement to sustain your environmental performance.
Can you tell us, Sébastien, what a simplified audit entails in just one sentence?
Once we’ve collected this data, what else can we do?
It seems to me that there are also interviews to be carried out with people in the field, in the factory, the production teams, isn’t that right?
The aim is to assess the maturity of the environmental performance of our plants, and to find out whether we’re at the stage where we’re paying our bills, or whether we’ve already put things in place (are we already ISO 50001?). These are very different stages.
Do some plants already have an energy manager to deal with all these issues?
What is the main benefit of improving the energy and environmental performance of an industrial plant?
How long does a simplified audit take?
Is a simplified audit mandatory?
Who can carry out the simplified audit, and what skills are required?
In a nutshell
Initial mapping gives you a synthetic, global view of all your plant’s processes and flows.
It allows you to:
1. Visualize all plant components, from raw materials to finished products, processes and utilities.
2. Finally, it lays the foundations for defining THE standard for your plant.
In short, initial mapping is the starting point for your industrial environmental transition.
Blog
Discover our latest articles
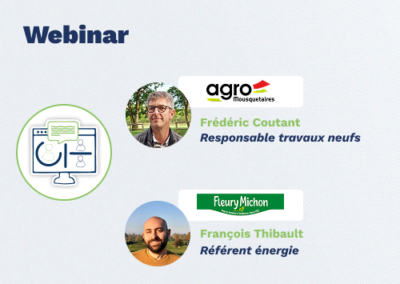
Webinar #5: How Etria optimizes its energy usage, reduces costs, and calculates the carbon footprint of its finished products
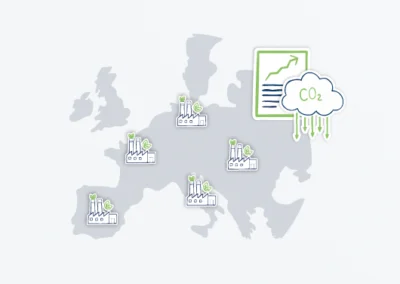